Production
High-quality shoe production
Every achievement comes with a key.
The key that opens the door to new challenges and allows us to overcome them.
Here at Giano the key lies in a happy marriage of the craftsmanship of excellent work and the legacy of a past that taught us the values and best practices for high-quality production; the strength of a flexible structure that can not only adapt to market demand, but also anticipate it.
Our strengths
You can count on us at every stage
To us, clients are not problems to be handled. They are part of our working structure, our approach to business. This is why we’re meticulous about every stage of the process, from design to order acquisition right through to shipping and after-sales care.
A state-of-the-art modelling and development department
Our creative team redraws the heart of artisan shoemaking with a view to the future. With all our partner companies, we work together to find ad hoc solutions that fulfil the increasingly exacting demands of the fashion world, but without compromising the brand’s origins.
Speed in step with quality
In our manufacturing, speed is of the essence. All our departments work in synergy to embrace and interpret market trends, turning them quickly into finished products. While never neglecting the care and quality of our work. Ultimately, the art of doing things well is exactly this.
How our shoes are created

Phase 1
Choosing the leather
The choice of hides is an essential task in the production of high-quality footwear.
At Giano we’re well aware of this, and that’s why we buy only the very best hides, mostly of bovine origin (cow or calf depending on the type of product and the size).
The hides undergo rigorous quality control. This is because being natural products, they may have minor defects which are eliminated in subsequent stages, or colour variations may occur during the tanning process.
We take great care to ensure that the hides we select are perfect in every way.
We constantly seek and commission new prints and colours from our supplier tanneries, in order to bring footwear and clothing into line.
We want the best; simple satisfaction is not in our DNA.
Phase 2
Cutting
This stage is the most wonderful expression of the meeting between tradition and technology.
This is where the real shoemaking happens, starting with cutting the selected materials: it all begins with the models created by the design department on the basis of shapes and features conceived by our designers.
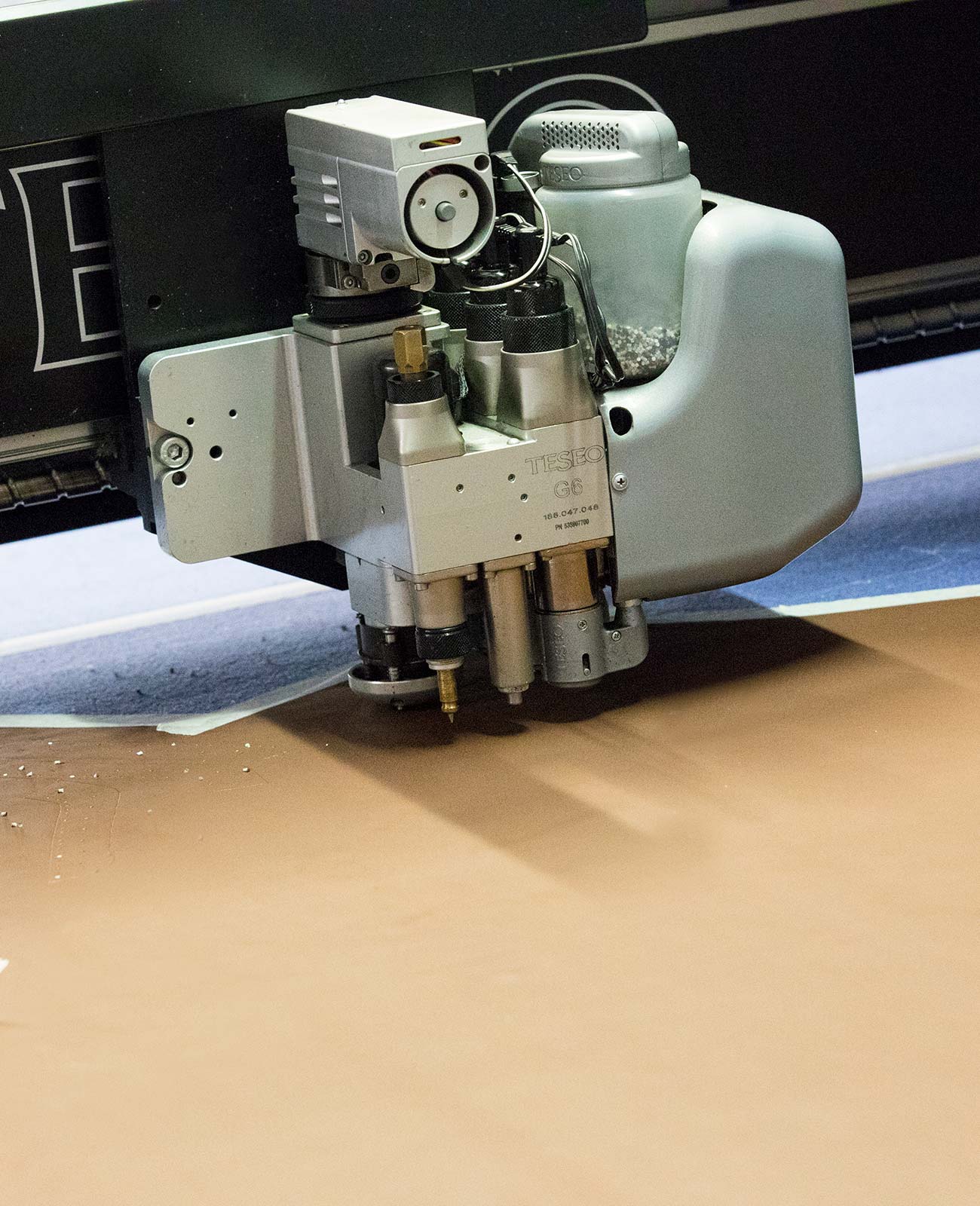
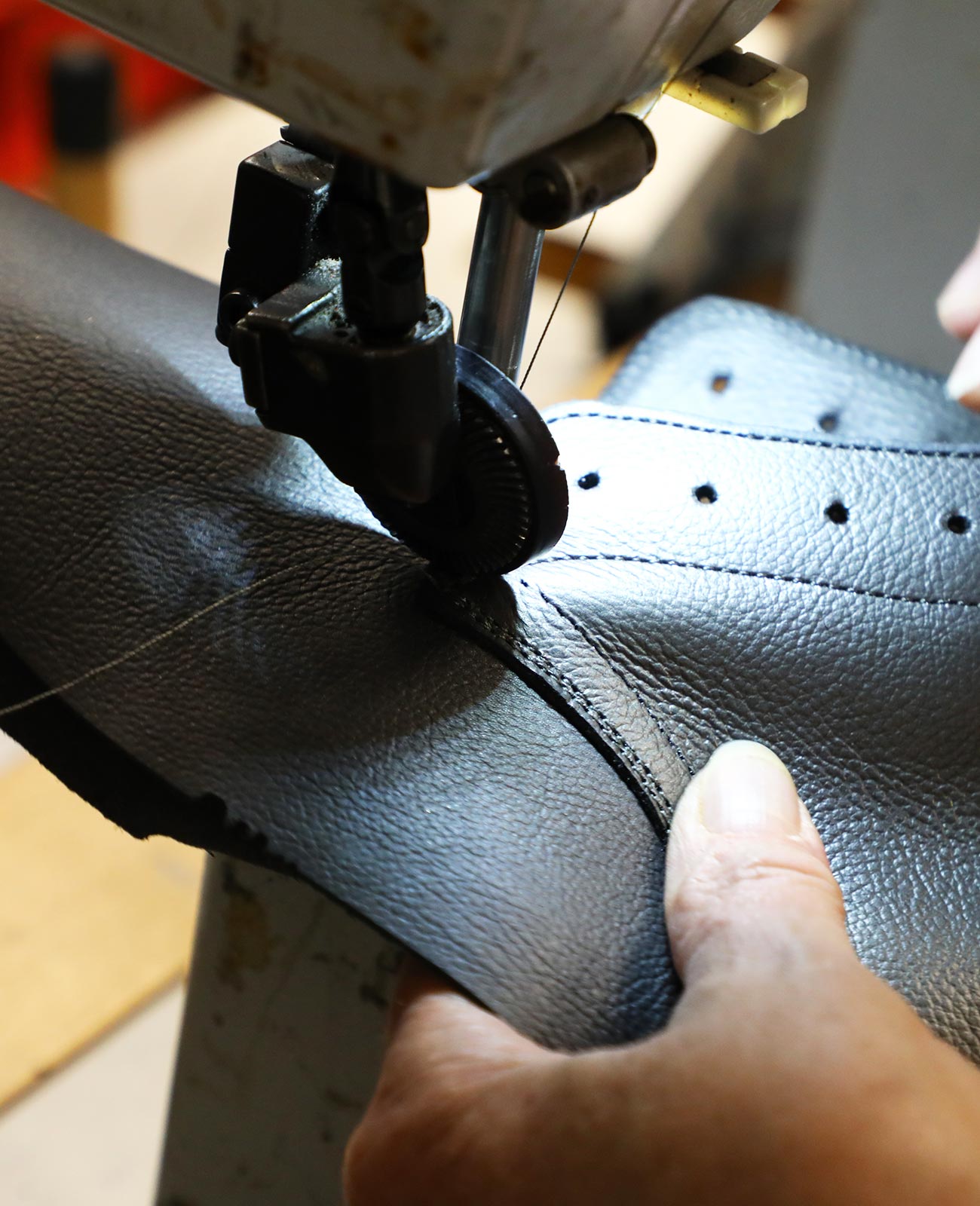
Phase 3
Binding
This is the stage when the cut pieces are arranged and assembled to form the upper.
The process starts by flattening the materials at the meeting point, and varies according to the type of material and the technique required. This operation demands extensive experience, because any mistakes may compromise the aesthetics and functioning of the shoe, and even lead to breakage of the upper.
Following this, all the pieces are sewn together to obtain the finished upper. Every pair of uppers contains an average of 15,000 stitches (depending on the model) and requires approximately an hour of labour to complete.
Phase 4
Assembly
This is when the upper and the sole are assembled.
To do this we use high-density plastic forms to which a footbed is fitted, depending on the model, which serves to hold the upper and the sole together. The footbed can be made of various materials. We select only the best natural materials to ensure comfort and breathability: real leather for formal shoes, felt for sneakers (which also feature a removable insole for even greater comfort).
The upper is then stretched over the form and attached to the footbed using machinery which assembles the front section of the upper and closes the rear section. The skill of the operator is essential, because incorrect placement of the upper on the form could result in a sub-standard product.
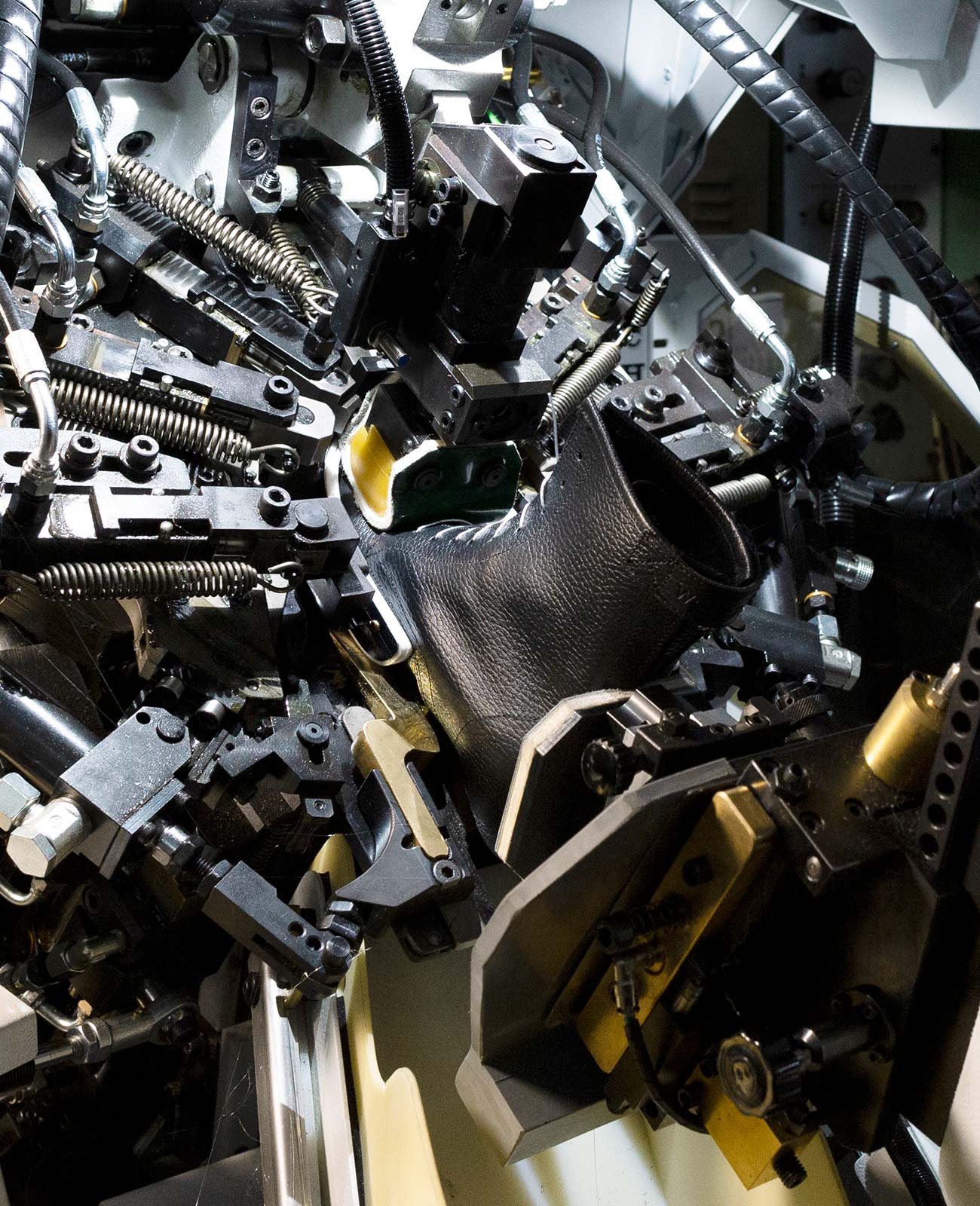
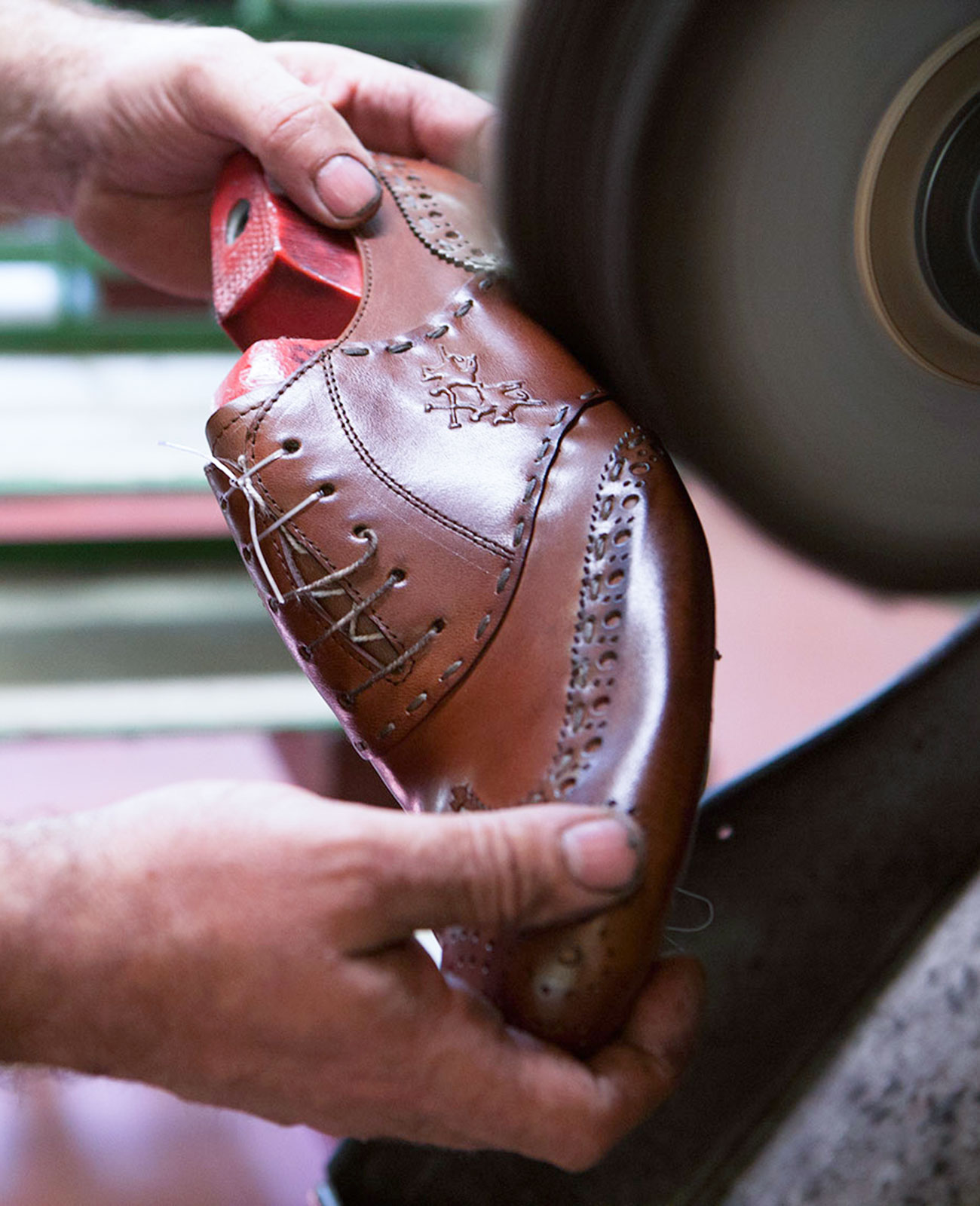
Phase 5
Antique finishing
Once the upper has been secured to the form, some leathers are given an antique finish to enhance their appearance.
Along with the final treatment, this is the most delicate artisan phase of the entire production process because it is strictly manual, and it is the skill of the worker that ensures correct application and evenness between the shoes in a pair.
Phase 6
Once the upper is assembled and ready, it’s time for the final stage: the application of the sole. In handmade shoes, this can be made from a range of materials with different characteristics. We prefer EVA soles (lightweight, tough and flexible) because they guarantee superb comfort while supporting the natural anatomy of the foot.
Every combination of leather and sole requires a specific glueing process to ensure a lasting bond. For this reason we use different types of adhesive and specialist techniques.
Each sole is designed for our clients using 3D-printed prototypes and then replicated with aluminium moulds, one for each size, for serial production. This operation may require months of fine-tuning and testing to guarantee lasting comfort.
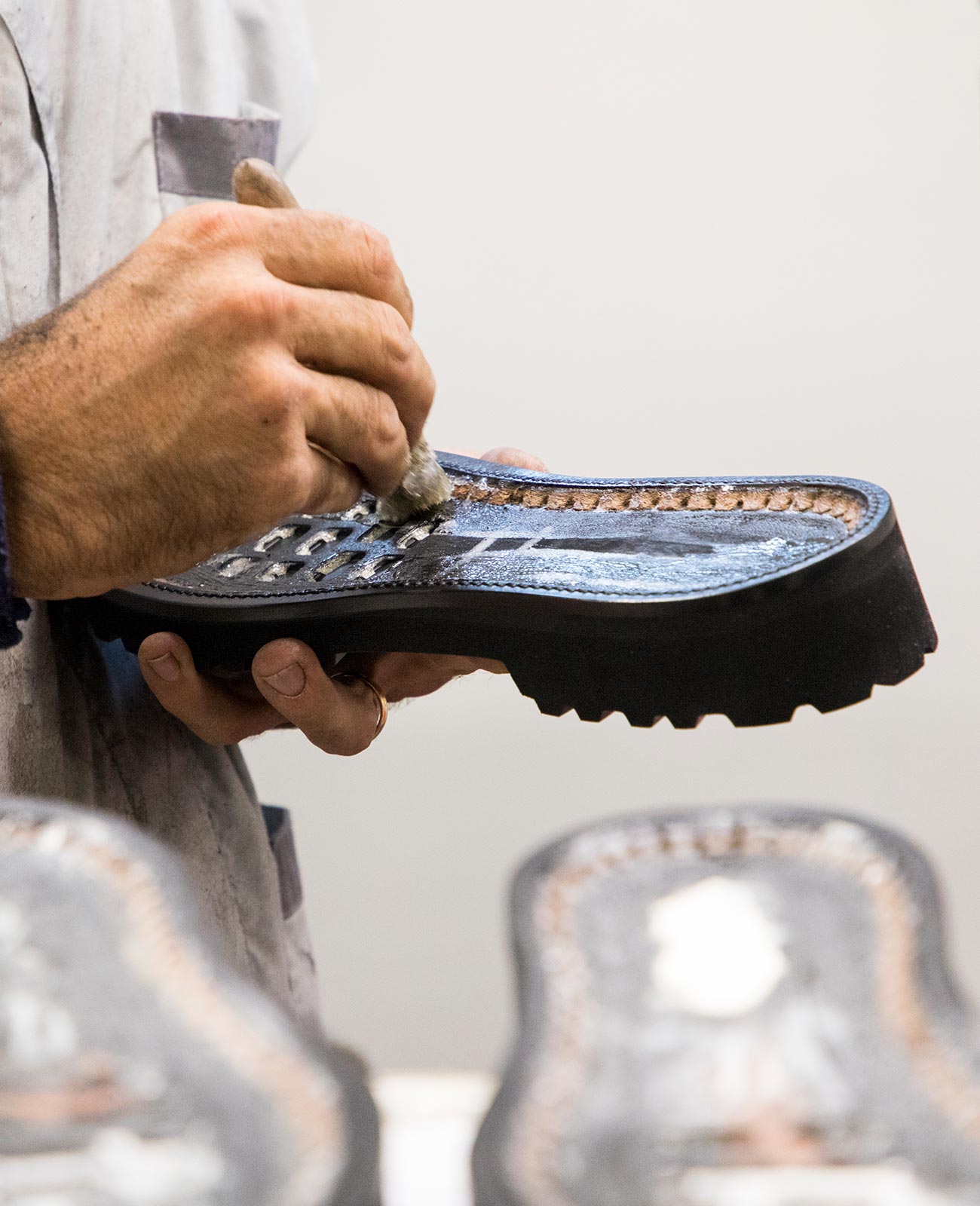
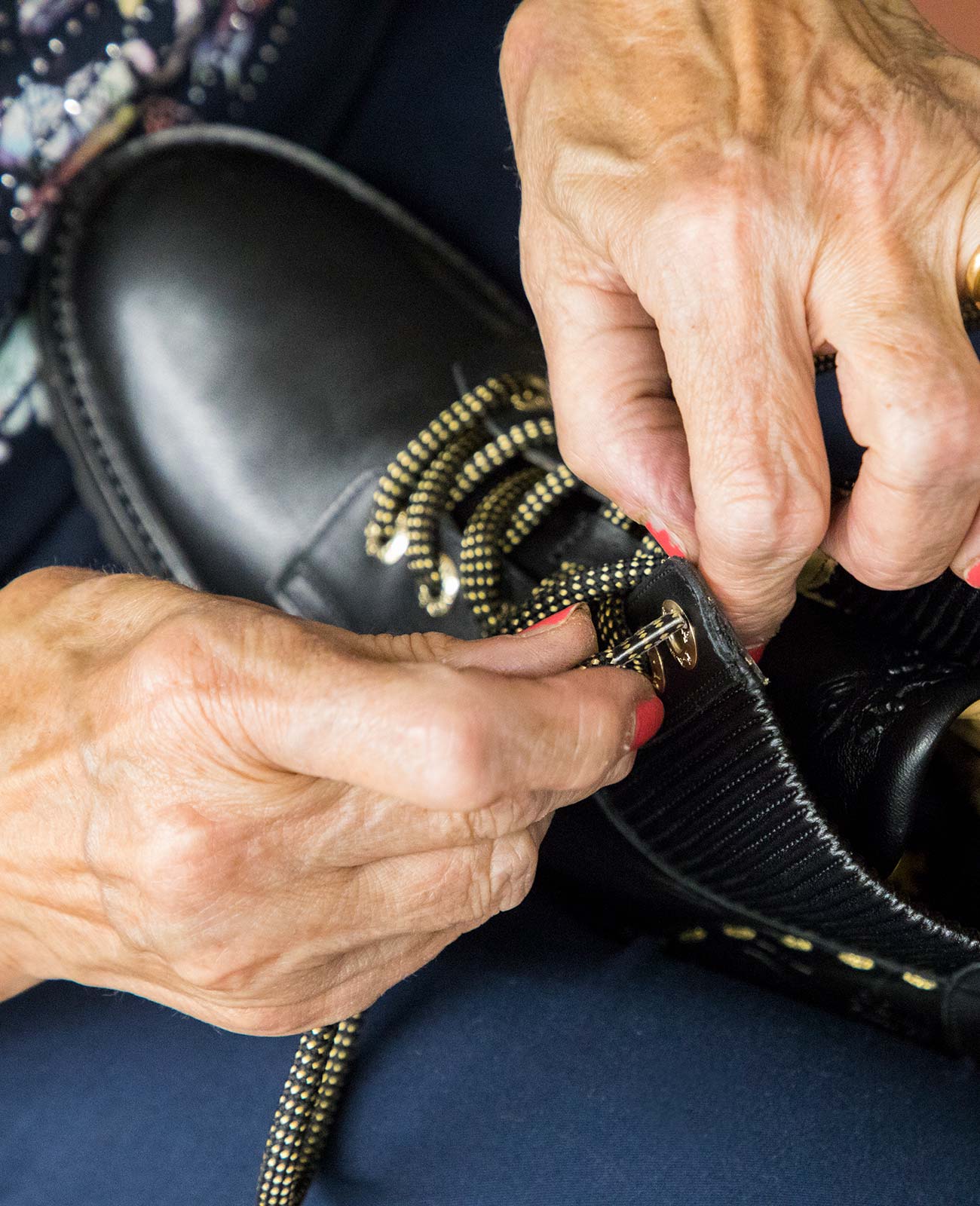
Phase 7
The finishing stage
Complete assembly of the shoe is followed by finishing, which includes removing any residue of adhesive and the more complicated and important finishing techniques using creams and rubs; this is done entirely by hand to enhance the antique appearance. The use of creams and the mixing of shades to obtain the most appropriate tone for the leather, along with the final polishing, is carried out by our experts, who bring the shoes to life.
Phase 8
Quality control and final boxing
As soon as the finishing is complete, the shoes are checked again one by one, to ensure they conform to our quality standards and avoid potential negative feedback from the end customer.
What is checked? For instance, that there is no colour variation between the left and right shoe, or that there are no flaws in the leather that escaped previous checks or emerged during the process.
If anything is not right, the product is discarded and we try and find out what caused the problem. Our idea of quality is synonymous with sophistication, elegance, style and comfort, the values we have built over time and continue to uphold in our work.
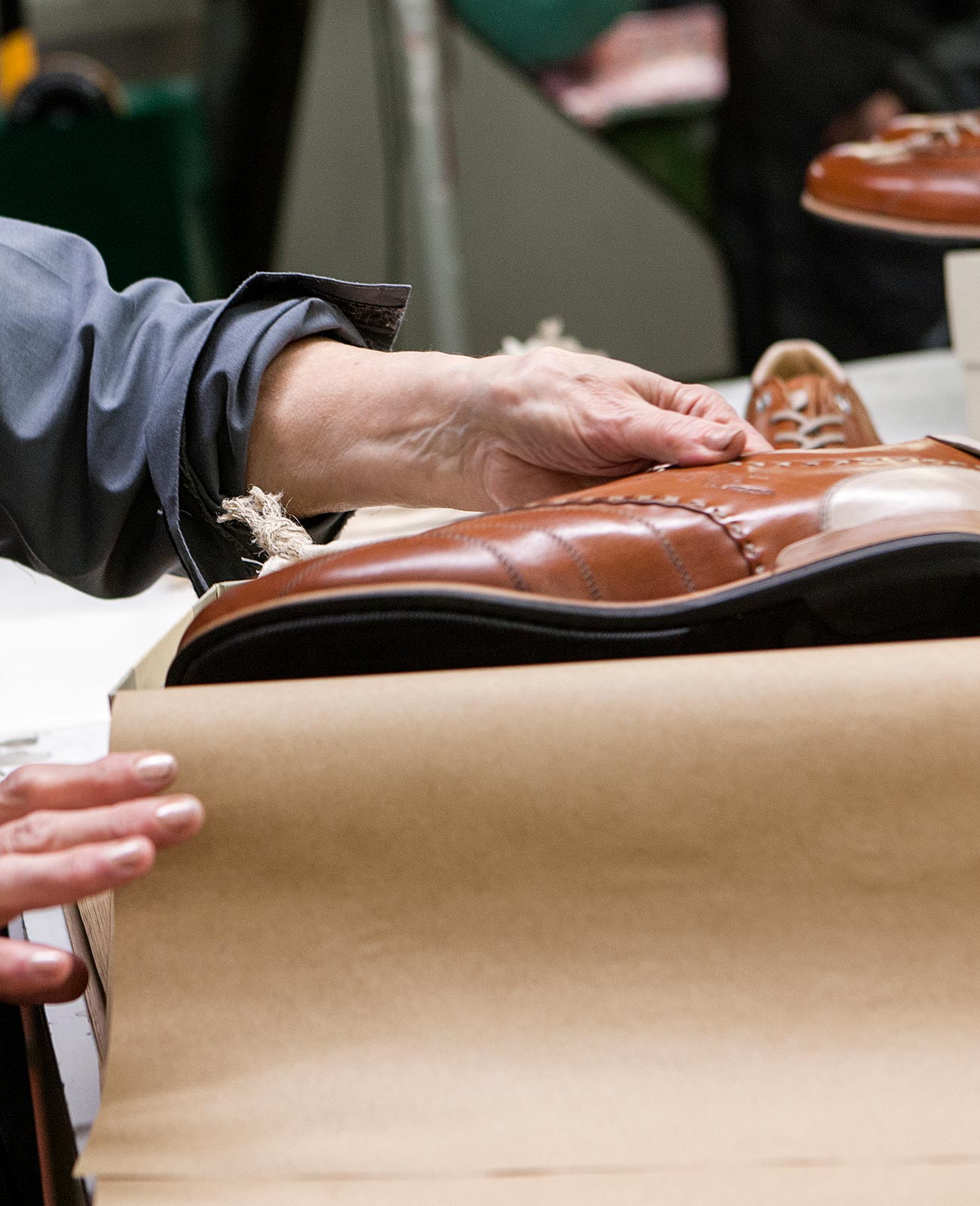